Failure of conveyor systems is a significant problem in the mining industry, causing extended downtime, lost productivity, and increased risk of fire.
The perils of a breakdown make proper detection and maintenance absolutely necessary for even the smallest of components within the conveyor system.
That’s where AutoTest’s BAMbino conveyor idler bearing monitor is valued highly: it proves that the life of every component can be effectively monitored and that with early detection, maintenance can be carried out without the costs and lost time usually involved in replacing conveyor bearings.
Australian Mining Review spoke to AutoTest managing director David Jenkins about the product.
BAMbino stands for Bearing Acoustic Monitor, and is the world’s first portable device that provides accurate, easy and early detection of faulty idler bearings. It earned an award of excellence in research from the Australian Coal Association, and two Engineering Excellence Awards: the national engineering excellence award for research and development, and the award for innovation. It is a handheld portable instrument that extracts bearing fault signatures measured from a distance of 0.1m to 3m away from the belt. A visual and audible alarm provides early notice of bearing damage, allowing forward planning of cost-effective maintenance.
It is a vast improvement on current inspection methods which involve highly subjective assessments without scientific evidence to detect faulty bearings.

According to David the BAMbino came into being after the team was asked to put together a monitoring system on Hamersley’s Mt Channar to Paraburdoo conveyor. “The Paraburdoo conveyor is about 25km long and has more than half a million bearings in it,” he said.
Like most systems reliant on bearings, conveyor bearings tend to have a typical bathtub curve, which sees many fail early on. The rest of the bearings will tend to last between five and 10 years, before they all start to fail again. Previously, with no way of telling which bearings would be the ones to fail early, it was practically impossible to fix in advance of a system failure.
David said in this instance, the biggest cost of bearings beginning to fail is not the bearings at all, but rather the belt being cut. “It’s expensive rubber, but the biggest cost is the loss of production,” he said. “It might cost two or three days of production, which costs hundreds of thousands of dollars in lost time. “So we wanted to develop a system that could predict an early failure of a bearing, before you can hear or see the failure.” The other issue impacting the Paraburdoo conveyor was its sheer length and the inaccessibility of certain sections, which rendered the traditional method of having an inspector walk down the line impractical.
“We developed a method of acoustically listening to the bearing and then we applied some signal analysis that we had used a lot and worked out a method of grading the bearing into good, bad and ugly,” David said. “The purpose of the device is not to tell you that the bearing is going to fail tomorrow, instead it’s about telling you that the bearing will fail in the next few months.”
When that has been achieved, the rollers or the conveyor section can be put into a program maintenance schedule, as opposed to having to stop the whole belt to fix the problem as was traditionally done. Roller sets, typically consisting of three rollers with bearings on either end of each roller, can be removed, repaired, and returned while the belt is still running at a low cost, without the risk of downtime.
However, if a bearing is allowed to fail, it can cause the whole conveyor system to seize. “The roller typically stops and the belt will wear that into basically a horizontal knife,” David said. “Ultimately, that will just cut the belt. “Now it depends on the exact mode of failure, but the alternative is that it ends up as a rotary knife.”

All of these problems can be avoided through early detection, now made possible with the BAMbino. The fast and effective handheld tool for predictive maintenance has a simple button operation via tactile membrane keypad with LCD display. The lightweight device screens out extraneous sources of noise, making it useable in highly reverberant underground tunnels. BAMbino is reprogrammable for up to 16 belt sections and is easily user-programmable. It also comes with threshold settings, a rechargeable battery and a 12 month warranty.
Most importantly, BAMbino comes with the peace of mind that bearings failures can be detected months in advance and fixed well before it becomes an expensive problem.
Having a Blast
AutoTest has also developed ground-breaking technology in the AutoBlast, which is a ground vibration monitoring and logging device. It can be used in various applications such as industrial vibration monitoring, ground transportation traffic vibration monitoring, construction site monitoring, noise, and vibration monitoring in a blasting zone.
It is also useful in the fields of earthquake engineering for monitoring the structures of buildings, bridges, and dams. Measurement is taken using a packet of velocity sensors, or geophones, and air overpressure level using a microphone, storing the data into a built-in memory storage, which can be downloaded to a computer via Bluetooth.
AutoBlast can be configured to perform a sensor check operation before monitoring starts to ensure the sensors are functioning properly. Events are automatically recorded when the measurement level of the vibration noise exceeds a threshold value, and alarms can be raised. These can be auxiliary alarms, such as a light signal or siren, as well as notifications sent by email or SMS using the built-in modem.
Keep Trucking
The team at AutoTest are committed to ensuring every piece of equipment on site is in full working condition. In addition to the BAMbino and AutoBlast, AutoTest offers a range of other solutions to guard against sudden equipment failure.
For example, AutoTest’s AutoStop Heavy brake meter is a decelerometer designed to test service and emergency brakes of heavy and slow-moving vehicles, off-road vehicles and even forklifts used in the transport and mining industries. The electronic in-vehicle brake-testing device is fully compliant with Transport Authority requirements. Portable and user friendly, AutoStop Heavy brake performance tester measures average and maximum deceleration, stopping distance, test speed and pedal force required to stop a heavy vehicle.
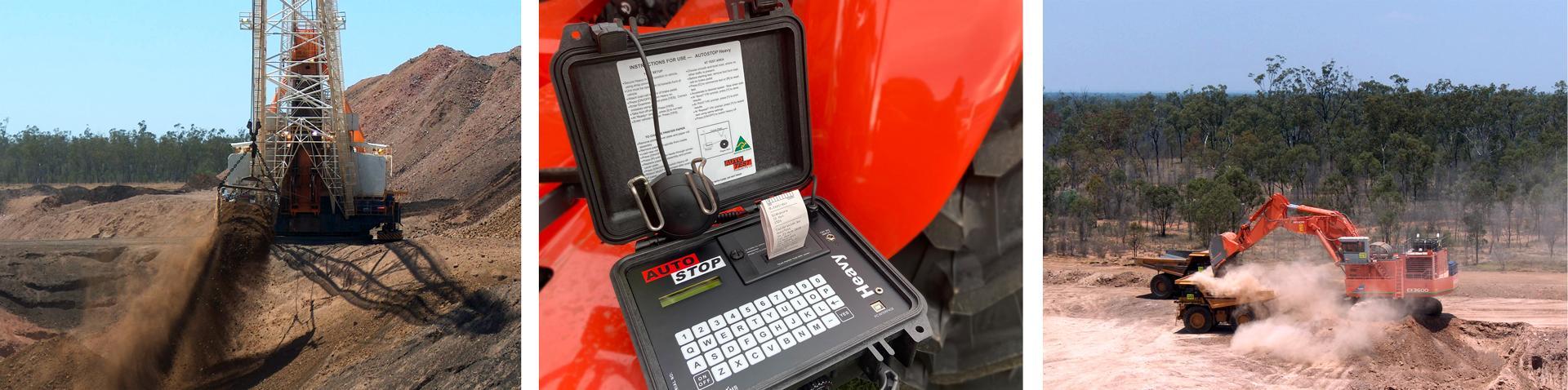
Once the vehicle has come to a stop, the brake tester evaluates the brakes’ performance and prints the results of the test. AutoStop Heavy comes with a data logging facility that allows stored tests to be downloaded to a computer for storage and analysis. It is capable of providing physical evidence of brake performance before and after any vehicle alterations, which mitigates risks. The AutoStop Heavy’s capabilities can be extended through the use of NetBrake, which is a database and brake test reporting software that assists the mining and heavy vehicle industries in Australia to manage brake test records, as well as brake test standards and calculations for fleets.
Finally, AutoTest’s combined AutoGas Five Gas Analyser and AutoSmoke Opacity Meter have been designed as user friendly analysis tools designed to improve how the gas efficiency of a vehicle is measured. Both are distributed throughout Australia and are suitable for both light and heavy vehicles. Battery operated, they measure the contents of the exhaust gas and assess the efficiency of a vehicles ability to reduce the amount of pollutant gases being released into the atmosphere. The combined device includes a built-in wireless connection between the AutoGas Five Gas Analyser and AutoSmoke Opacity Meter. Smoke tests can be carried out using a computer connected to the Gas Analyser, which provides easily read, onscreen measurement data.
GET A QUOTE and contact us today.
About AutoTest
AutoTest was founded in the early 1990s as part of Vipac Engineers and Scientists. The idea behind its foundation was to commercialise intellectual property developed out of the consulting business, however, AutoTest branched out on its own in 2000 and since then is a truly standalone operation.
It is now an award-winning Australian made and owned manufacturer and distributor of state-of-the-art automotive testing and diagnostic products based in Kensington, Victoria, possessing ISO 9001 Quality Management System accreditation. AutoTest’s products have been designed to provide many years of reliable testing and have been built from durable quality components. Its products are currently used by garages, workshops, regulatory authorities and service testing stations.
AutoTest supplies directly and through a network of international distributors across Australia and the world. Its development program ensures the consistent launch of innovative, new products to meet industry demand, from BAMbino to the AutoMonitor and everything in between. -AMR
GET A QUOTE and contact us today.
Published in Australian Mining Review May 2021